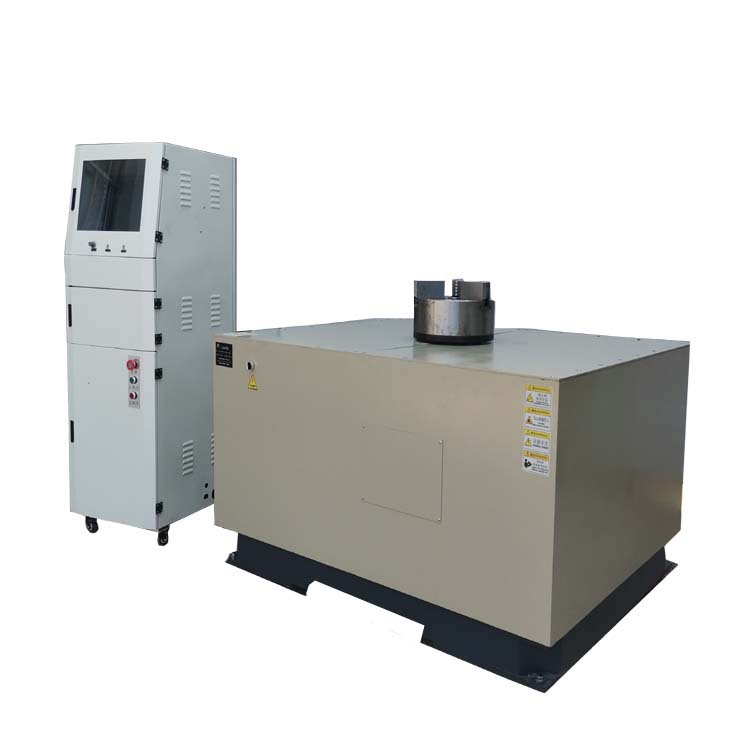
YLD-2000A vertical dynamic balancing machine
Brief introduction:1、 Product IntroductionThis series is a single-sided vertical balancing ma
1、 Product Introduction
This series is a single-sided vertical balancing machine, suitable for dynamic balancing verification of disc-shaped rotating parts on a single side. It is an ideal equipment for dynamic balancing verification of fan blades, ventilation fan blades, automotive flywheels, clutches, brake discs, brake drums, hydraulic torque converters, hydraulic couplers, and other parts. Simply replace the furniture where the workpiece is installed to perform balancing verification. The ordinary model of this machine is driven by a dual speed motor, while the "A" model is a variable frequency speed regulation system. It is processed by an industrial control computer, and the LCD display shows the imbalance value, phase angle, and real-time speed in real time. It is equipped with an industrial cabinet and forms a balance machine system with the mechanical part, which is convenient for parameter storage and printing. The system has high testing accuracy, reliable use, convenient maintenance, and is more advanced than other testing systems. It can be equipped with specialized fixtures such as universal fixtures and torque converters, as well as accessories such as side weight removal drilling machines, vertical weight removal drilling machines, and vacuum cleaners.
二、Main technical parameters
1. Host parameters
model | YLD-2000A |
Measurement time | 10s (measurement period can be set arbitrarily) |
Software version | Windows XP |
Display method | 19 inch LCD display |
source | Three phase four wire AC 380V, 50HZ |
Working mode | continuity |
Maximum mass of workpiece (Kg) | 2000 |
Maximum diameter of workpiece (mm) | 1500 |
Motor power (KW) | 11 |
Reduction rate of imbalance% | ≥ 90 |
Minimum reachable residual unbalance (emar) | ≤ 3g ? mm/kg |
2. Industrial computer parameters
Speed range: | 100 rpm -1000 rpm |
Phase error: | Measuring error with standard signal<0.3 o |
Amplitude error: | Measuring error with standard signal<1/1000 |
Storage rotor number: | 255 |
Angle decomposition number: | 60 |
Maximum power consumption of the entire machine: | 200W |
三、Product features
The GB-2000 universal microcomputer balance measurement system is the latest universal microcomputer balance measurement system under the Windows XP operating system, and the operating environment of this system must be at least Windows 95 operating system or above. The hardware of the system consists of multiple single chip microprocessors (CPUs), using dual high-speed A/D converters. It has functions such as programmable tracking amplification, programmable tracking filtering, real-time speed measurement, real-time data transmission, analog reference signals, and analog vibration signals. It fully utilizes the advantages of Windows, making the measurement system incredibly powerful. From the operation interface, data processing, report printing, data graphic display, and file graphic printing output, all reflect the charming style of Windows. Focused design makes the balance measurement system suitable for various types of balance equipment such as soft support, hard support, static balance, dynamic balance, etc. And can achieve a measurement system to simultaneously measure multiple balancing devices. The full dynamic and uninterrupted measurement of the magnitude, phase, and speed of the imbalance has been achieved, greatly improving the measurement accuracy.
Principle of measurement system structure:
The strength of the electrical signal output by the vibration sensor directly reflects the magnitude of the imbalance of the workpiece, but it also includes many high-frequency interference signals caused by reasons such as bearing operation, machine vibration, belt transmission, etc. These signals are input to the pre-processing board to filter out the high-frequency interference signals and amplify the useful signals. The system signal amplification adopts automatic (or manual) amplification, and the microcomputer automatically selects gears based on the size of the sampling signal to adapt to high-precision requirements and the balance of large initial imbalance workpieces. When the magneto electric sensor approaches the marked steel plate on the balance machine spindle, it is induced to generate an electrical signal. When the rotor rotates once, the magneto electric sensor generates an electrical pulse. (Note: When the rotor rotates once, the magneto electric sensor should only emit light once.) This type of electrical pulse with the same frequency as the rotor is also input to the pre signal processing board for shaping, and is decomposed into two signals, one for operation with the vibration signal and the other for measuring the speed.
Finally, the pre signal processing board inputs several collected and processed signals into the industrial control computer motherboard through a data cable, which is controlled by software for data access, calculation, and display. Industrial computers have the following important tasks:
(1) Control the acquisition and access of vibration signals and photoelectric signals;
(2) Decompose the pulse signal of the photoelectric sensor and obtain the current test speed of the workpiece through one path in the decomposition;
(3) Compare the left and right vibration signals with the decomposed photoelectric signals to obtain the phase signal. This signal represents the orientation of the imbalance on the measurement surface.
(4) Calculate the magnitude and angle of the imbalance on the workpiece based on the stored system calibration coefficients and collected on-site signals